So I thought bleeding the brakes would be a walk in the park. How wrong I was.
It's surely partly my fault for not checking everything before starting the bleed, only if I knew I've been sold a set of junk part.
Turned out one front caliper had a damaged seat, but that one could be repair with a drill bit and some caution.
The rear calipers were another story. The seat of the bleeder were actually gone for good. They actually had been drilled out, no kidding.
See for yourself :
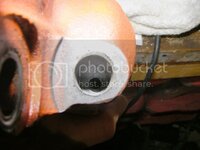
This is the caliper after we redrilled it to accept a 1/4 NTP repair fitting, you see that crescent shape in the bottom, that's the remain of the bubba's drilling.
I don't know what was the idea, and I don't want to....
Here's the bleeder once repaired :
The repair fitting is machined out of a regular NTP plug, couldn't find one locally and didn't to wait for an online order.
Worked well.
So now I can actually start the build.
Make a "ghetto" speed bleeder :
The cutout in the middle is for the pression to go in both reservoir, saves me a fitting.
All went nicely.
The whole system was empty dry so as advised by forum member I will do a second bleed. I first let it sit for a while, will then gently whack all the lines to remove any air bubble, then bleed again.
I also filled my PS pump, and started to "prime" the system with that :
Sure I can't get much pressure with it, but still I can make the fluid circulate. I'll wait to have someone around to operate the steering box and the hydroboost while I do that.
Last problem solving : my rear rims.
I have 10.5" rim at the back (8" at the front). Originally it was mounted with a small Mr Gasket 1/4" spacer. I was told it's not the best setup, so I looked for proper wheel adapter.
I was given a set of 1" adapter, nice and sturdy but is made my wheels really sticking out of the body : I would need a flare job.
So I decided to rethink from the start : why the 1/4" spacer? Because otherwise the rims would hit the calipers. I checked and it was hitting by not much, 0.15" at worst.
So I took the wheels to my best machinist and I had this 0.15" removed from the wheel itself.
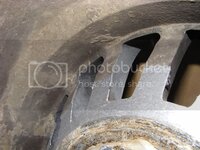
Now the rims are fitting much better, barely sticking out, I can live with that, and I'm saving months of fiberglassing.
Never like flares on Vette anyway.
That also gave me the occasion to learn how to operate that antique tire changing machine he had in a corner of his shop, and did put my summer tires on my DD while I was there.