phantomjock
Well-known member
Went a little sideways yesterday.
After mounting the Rear Wheels/Tires, the spring on the coilovers is up against the tire. BUGGER!
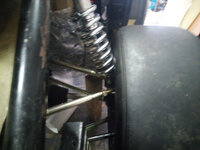
Top view shows the same. The one plus side - it resolves how to mount the shock to thwe cage - drill or weld - now neither!
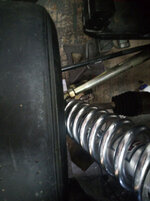
I'll get on the corner weights anyway. I dug out the 2" wheel spacers and put those in. More than enough clearance to do the job.
The obvious fix will be a bit of construction - another Pushrod setup. Worked CAD this am - should be straight fwd, just time...
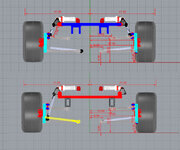
The preferred option at this point is the lower drawing. Time and measurements will dictate.
Not TWO forward and ONE back. One Sideways! And another one forward.
Cheers - Jim
After mounting the Rear Wheels/Tires, the spring on the coilovers is up against the tire. BUGGER!
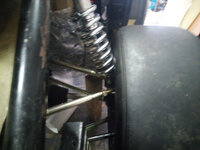
Top view shows the same. The one plus side - it resolves how to mount the shock to thwe cage - drill or weld - now neither!
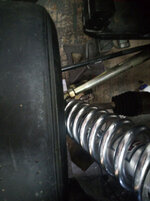
I'll get on the corner weights anyway. I dug out the 2" wheel spacers and put those in. More than enough clearance to do the job.
The obvious fix will be a bit of construction - another Pushrod setup. Worked CAD this am - should be straight fwd, just time...
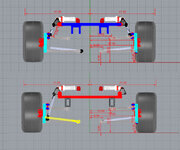
The preferred option at this point is the lower drawing. Time and measurements will dictate.
Not TWO forward and ONE back. One Sideways! And another one forward.
Cheers - Jim