rtj
Well-known member
- Joined
- Nov 5, 2011
- Messages
- 3,381
Small progress, brace and hat installed.
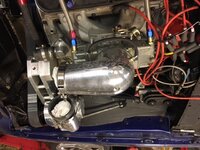
Made steel bulkheads for the rad support 4.5” id. Also, made an alum stand off for the BOV. I tacked it up then chickened out welding it ( don’t want to melt it down!). Need a few more days of practice doing 1/4” t-joints to get confident in my settings and skill.
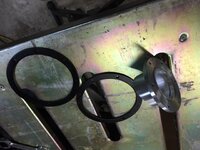
Made an adjustable fence for my HF bead roller. One sided fence only means you can only crank one way while working the metal. Intercooler inlets and blower 180. I may make billet intercooler inlets, not sure.
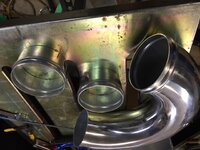
I have to learn to plan better, switching back and forth with the vice and rotary table gets old fast.
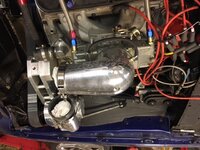
Made steel bulkheads for the rad support 4.5” id. Also, made an alum stand off for the BOV. I tacked it up then chickened out welding it ( don’t want to melt it down!). Need a few more days of practice doing 1/4” t-joints to get confident in my settings and skill.
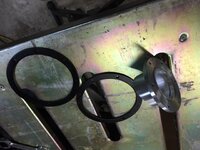
Made an adjustable fence for my HF bead roller. One sided fence only means you can only crank one way while working the metal. Intercooler inlets and blower 180. I may make billet intercooler inlets, not sure.
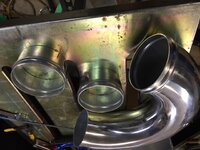
I have to learn to plan better, switching back and forth with the vice and rotary table gets old fast.
Last edited: