bobs77vet
Well-known member
I do recall that episode, I have a planishing hammer and an English wheel and can use them on this, maybe slice it, stretch it then press it, well you guys got me thinkingNext time I do this, I'm going to try a trick that I saw on Bitchin' Rides. They pretension the metal where they're going to make the louver (aka stretch the metal by hammer and dollying the place where the metal is going to be louvered).
Grand pa plays with the 4 yr old grand daughter in the garage with kinetic sand all the time
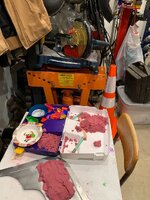
Why not make a casting mold from clay that hardens
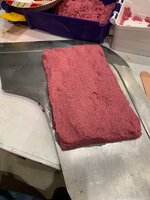
I can push the clay into the louvre so I actually make a bottom die and then repeat for the top die
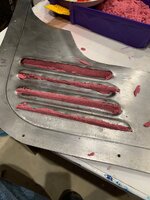
And I think it would work
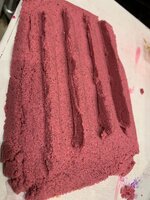
Now I think the sweet spot is making this for one full louvre opening both up and down with the intermediate flat spaces My panels are handed and mirror images so one die only works for one side, where there are 6 repeatable louvres
So I think I use a clay mold then use the epoxacast to make a top and bottom die. The problem I have is when I hammer and dolly one side the other side distorts, perhaps the first strike is with the dies I made first and then the finishing press is with the full die to make both sides pressed at the same time , thanks everyone for the tips and websites, I have always wanted to learn about casting things
Last edited: