vette427sbc
Well-known member
Next project for my '69 is to try to incorporate a Tilton balance bar into the stock(ish) pedal box area. There are balance bar setups that would be bolt in but I dont like that the whole assembly is outside of the firewall. The plan is to modify the pedal assembly to allow for the balance bar to attach direct to the pedal (like it should) and put two master cylinders on the firewall. Ill also be changing the stock manual ratio from 5.4:1 to 6:1.
As much as Id love to just buy a lightweight forged aluminum firewall mount pedal box from Tilton or the other companies out there, there are two issues with that (for me):
Cant keep the pedals in the same location (left/right) as stock because I want to keep a 2" diameter steering column and the brake pedal is centered under the column.
The pedal boxes are all short by ~2" to reach the firewall if I want the pedals in stock location (forwards/back) (I do)
Time to start cutting
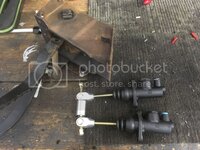
As much as Id love to just buy a lightweight forged aluminum firewall mount pedal box from Tilton or the other companies out there, there are two issues with that (for me):
Cant keep the pedals in the same location (left/right) as stock because I want to keep a 2" diameter steering column and the brake pedal is centered under the column.
The pedal boxes are all short by ~2" to reach the firewall if I want the pedals in stock location (forwards/back) (I do)
Time to start cutting
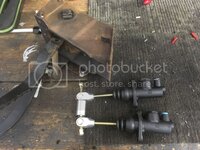