phantomjock
Well-known member
There are a few threads on tilt-front ends, thought I'd add my efforts and progress so far.
To begin with - I pealed and pulled the front clip and traded it off for a tilt setup.
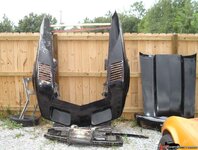
Can't say it was a great deal - but I didn't want to mess with "flogging"all the bits.
I got it home on a borrowed trailer:
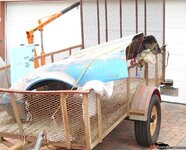
Set up in driveway and pealed and stripped:
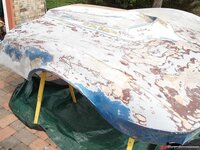
You all know that can be revealing process. Here are some cracks and damage I'll need to deal with:
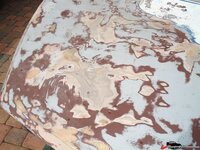
Flipping over I found my first BUBBA!
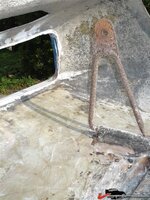
If you look closely its bent steel barstock, with a welded tab. Note, the back isn't even welded to the piece 'glassed in! More bubba on the other mount too:
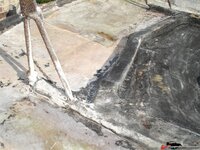
I removed the hood frame (lip) to clean up and re-enforce the whole clip.
LOOK DARLIN' MO-BUBBA! Some mighty-fine choice in composite filler:
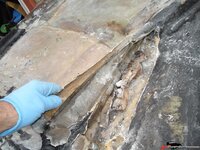
Man - What bunch a Bubbas built this thing?:stirpot:
OMG! Its a
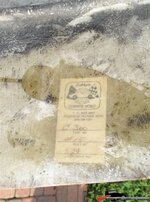
Ok- Ok - its a "wreck-lers." But it is an early one (#15) so maybe they figured out a better filler for this spot!
Having messed about in boats a long time - I am a bit of a composites engineer - so I wanted a stiffer, stronger set up without too much added weight.
Next step making some templates for a composite core layup:
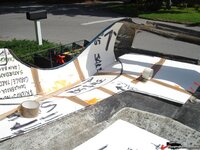
The templates were used to cut and shape Balsacore:
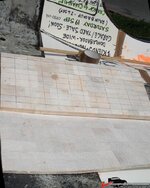
Next it was suit up and Lay-Up:
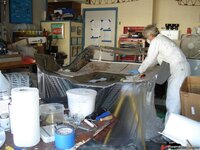
All that was followed with a vacuum-pull to laminate the core to the frontend, then layups (again under vacuum). The project is on hold but once I get through some house renovation, I'll get back to it.
Cheers - Jim
To begin with - I pealed and pulled the front clip and traded it off for a tilt setup.
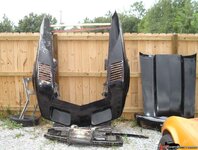
Can't say it was a great deal - but I didn't want to mess with "flogging"all the bits.
I got it home on a borrowed trailer:
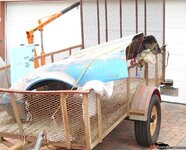
Set up in driveway and pealed and stripped:
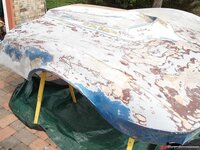
You all know that can be revealing process. Here are some cracks and damage I'll need to deal with:
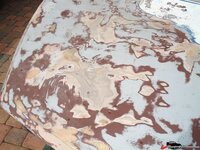
Flipping over I found my first BUBBA!
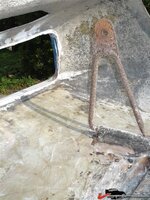
If you look closely its bent steel barstock, with a welded tab. Note, the back isn't even welded to the piece 'glassed in! More bubba on the other mount too:
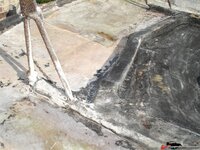
I removed the hood frame (lip) to clean up and re-enforce the whole clip.
LOOK DARLIN' MO-BUBBA! Some mighty-fine choice in composite filler:
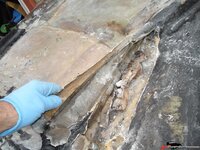
Man - What bunch a Bubbas built this thing?:stirpot:
OMG! Its a
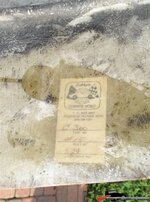
Ok- Ok - its a "wreck-lers." But it is an early one (#15) so maybe they figured out a better filler for this spot!
Having messed about in boats a long time - I am a bit of a composites engineer - so I wanted a stiffer, stronger set up without too much added weight.
Next step making some templates for a composite core layup:
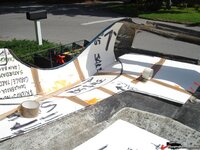
The templates were used to cut and shape Balsacore:
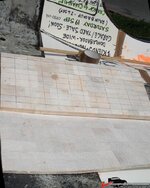
Next it was suit up and Lay-Up:
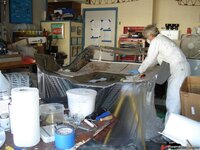
All that was followed with a vacuum-pull to laminate the core to the frontend, then layups (again under vacuum). The project is on hold but once I get through some house renovation, I'll get back to it.
Cheers - Jim