Hi again,
Back after a long vacation and also a period of work in South Africa...
Time for the engine now. Restored by the previous owner but I just could not keep my hands from it.
Found a few loos bolts, leaking gaskets, a cheap cam gear set, 2 broken piston rings and a badly machined crank. It was starting to chip metal from the bearings, not good:suspicious:
Since this is the cars original engine I did not want to make any drastic changes. I am planning on building a completely new engine in the future based on new parts.
Anyway, this is the to do list:
-Line honing
-Top decking
-polishing of the crank
-Clevite 77 bearings
-File Fit Moly rings (Speed pro)
-Keep the pistons
-Hone the bores (very little, engine already bored 0,030" and within tolerance)
-Fix the rods
-Macine the heads
-polish the valve seats/valves (valve job and guides done by the prev. owner)
-Roller timing set
-Change the original farm tractor cam to a Comp Cams XE268H shaft
-Comp lifters
-Comp valve springs
-Comp Magnum rockers
-ARP studs
-Melling 77HV oil pump
Nothing fancy, it will be a nice machine with some more punch compared to the original configuration.
Test assembly of the ARP studs. Nice quality of the ARP stuff! Those of you with a sharp eye will spot a mistake mad by me in this photo...
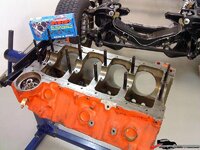