69427
The Artist formerly known as Turbo84
I've been welding up (TIG) my aluminum lower radiator crossmember, and am just amazed at the amount of heat required to do the welds. The new crossmember is quarter inch and 3/16 inch material, and obviously needs a bunch of current for a while to get things heated up, and during the welding, the heat spreads throughout the whole thing . (Below is an early mock up photo during construction.)
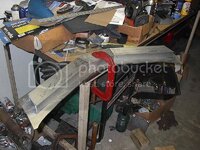
In one of the hardware stores where I go to I've seen aluminum stickweld rods. Anybody ever stickweld aluminum? My experience with stickwelding steel is that you can put down a bunch of heat and move pretty quickly. I would expect the aluminum rod to be consumed quickly, but would it allow a quicker weld and prevent a lot of the heat from just conducting off to the rest of the part? I'm also unclear about the bead strength compared to the TIG bead.
Any learned opinions?
Thanks,
Mike
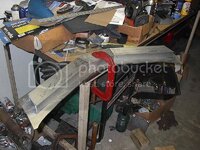
In one of the hardware stores where I go to I've seen aluminum stickweld rods. Anybody ever stickweld aluminum? My experience with stickwelding steel is that you can put down a bunch of heat and move pretty quickly. I would expect the aluminum rod to be consumed quickly, but would it allow a quicker weld and prevent a lot of the heat from just conducting off to the rest of the part? I'm also unclear about the bead strength compared to the TIG bead.
Any learned opinions?
Thanks,
Mike