Okay, here is that huge update I have been procrastinating on for the past week or so.
First I am going to start by rewriting my posi assembly tutorial - I found there were too many mistakes in the old one. I learned everything from Gary:thumbs:
First, take your posi case and polish it using a carbide burr, dremel tool, sandpaper and any other tools you have which you think will work - you want all those rough edges gone, as this reduces stress cracks caused by all that torque put out by the motor. Polish the internal seems as well. Stay away from the area where the spider washers are; I use duct tape to protect these surfaces during polishing.
Here is what the case looked like before polishing...
After polishing for about 2.5 hours (only good pics I have are with it partially assembled)...
Look closely at the internal seams I polished in the back of the case...
If you plan on using ARP ring gear bolts with your rebuild, now is the time to countersink the holes on you posi case. Gary touched base on this in one of his posts. Basically, what he found was there was a shoulder on the ARP bolts which prevented them from seating flat. The case I bought from Gary already had the holes countersunk, so that saved me from having to do it. A step drill might work to slightly countersink the holes too, but you'd have to ask Gary about that one.
The next step is to bevel the edges on all of the gears in the posi case. I used a dremel grinding stone and walked it along the edge. The reason for this is because of the backlash you will be setting the case with. You want the case to turn smoothly after you are done - bringing the backlash on the gears to a minumum causes binding on the edges of the spiders. Remember, just walk the dremel - do not remove a lot of material.
The next thing you want to check is the king pin that goes through the spider gears. I bought a used one from a vendor and found out it was worn:bs . I bought a new one from Gary - he sells an oversized one for the posi case. The OD of the pin should be 0.747 (I think that's what it is, I'd have to check). The ID of the holes in the posi case I think are 0.749. Gary sells an over sized cross-shaft with an OD of 0.748. Its a little bit of a tighter fit, which is a good thing. That's the one I used in my rebuild.
I clean everything with brake cleaner and compressed air. The next step is to sort out the clutches. They are stamped differently on each side. If you draw you fingernail around the edges, you'll immediately know which side has the deeper stamping. Take a sharpie and put a small "d" on the deeper face so you don't have to keep checking when assembling. The marker will eventually wear off from the oil, but it will keep you organized. I asked Gary as to whether it mattered which way the two clutch packs faced (do all the deep stampings for both sides need to face to the left, or to the right). He said it didn't matter, but you need to keep the deep faces facing in one direction for each clutch pack. Lay all your parts onto a clean rag - once again, this will keep you organized.
Alright, here is where all the patience on this project comes in - figuring out which size shim is required to set up the posi case. Here is a shot of all the shims that came in Gary's kit...
Start off with a 0.040 shim on each side of the casing. Chances are it is going to bind, but you've got to start somewhere, right? My definition of binding is that you turn the case and it turns, but you've got to apply a lot of pressure to get the spiders moving...I hope this makes sense. I have made of video of when I was originally setting up my spiders - this is what is considered extreme binding...
[ame=http://s6.photobucket.com/albums/y232/MGT-inator/?action=view¤t=MOV02516.flv]
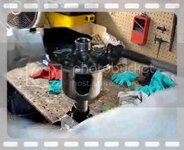
[/ame]
Once you install all the gears and shims in the casing, you want to seat the clutches. on each side. Do this by rotating the posi case about 50 times per side using the spanner wrench you made. When it comes to setting up the posi case - paience is a virtue. You need to get inside Gary's head and feel what he's feeling, it took me a really long time to understand what he was trying to explain to me. Lets say the 0.040 shims are too tight. The next thing you want to do is take those shims out and replace them with 0.035 shims. Seat the clutches again using your homemade spanner wrench. Next, take your bare hands and try rotating the posi case. Try it on one side, then flip it over and try it on the other side. If you are not able to turn the posi case by hand smoothly, then you need to try some 0.030 shims. Do exactly the same thing - seat the clutches, then try rotating each side using your bare hands. You want the feel to be smooth - you will feel a slight spider gear bumpiness, but it will be faint. If you don't feel a slight bumpiness, then that means the gears are now too loose. Basically, what this tells you is that the shims sizes you need are between 0.030 and 0.035. You need to figure out which shim for both sides is needed. They may be different sizes - it depends on the posi case.
So now you have figured out which size shims are too tight and which size shims are too loose. The next step is figuring out which size shim is needed on each side of the posi case. When I rebuilt my case, I found that a 0.035 shim on both sides felt a bit different (the side which is on the yokes is the one you are basically testing for tightness). With the ring gear side on the yoke, I turned it with my hands and found it to be pretty darn close to what I wanted; but when I flipped the casing over and tested the other side, I found it was a little bit tighter (but they were both 0.035 shims...so what gives?). This meant that the machining of the casing was a bit different on each side. Thus, the shim sizes were going to be different (so I only needed Gary to grind up one set of shims for me, both sides weren't going to be the same size). I had Gary grind me up one each of the following shims: 0.031, 0.032, 0.033, and 0.034. The shim I had in there was a 0.035 shim and that was a little bit too tight, so I swapped that one out for a 0.034 shim and tested both sides again. The feel of both sides now felt exactly the same. I left it at that. The final shims I used were a 0.034 shim and a 0.035 shim.
Will update more tonight