I am going to attempt my first fiberglass project (other than just fiberglass repair). Would like some suggestions on how to do this. Obviously it needs to be structural at underhood temps and the slight vacuum created by the pull of air through the filter.
I figure that I can make cardboard splines from cross sections of the CAD model and glue foam in between. Then shape it, cover it with acrylic tape and fiberglass over the top of it. I understand that the blue foam used for insulation shapes pretty well and the core can be dissolved out with acetone.
Any suggestions are welcomed. The longest length of the airbox is 25 inches.
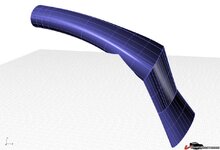
I figure that I can make cardboard splines from cross sections of the CAD model and glue foam in between. Then shape it, cover it with acrylic tape and fiberglass over the top of it. I understand that the blue foam used for insulation shapes pretty well and the core can be dissolved out with acetone.
Any suggestions are welcomed. The longest length of the airbox is 25 inches.
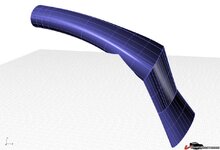