69427
The Artist formerly known as Turbo84
As the title implies, I don't have a lathe. However, I'm trying to do some grinding/reducing of the OD of a distributor piece (the points cam).
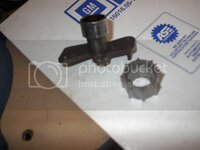
I'd like to chuck it up in my drill press to spin the thing, and then make a grinding/sanding fixture to remove the cam bumps and a bit of the OD. To give you some idea of what I'm looking for (unless there's something a bunch better) I need something with perhaps a 1/2" shaft (to fit my drill) and two cones that slide over the shaft to center the cam piece bore (that the distributor shaft slides through).
Any thoughts or suggestions? This is just an experimental project at the moment so I don't want to spend serious money at a machine shop.
Thanks,
Mike
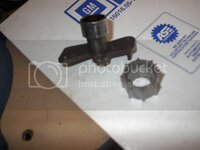
I'd like to chuck it up in my drill press to spin the thing, and then make a grinding/sanding fixture to remove the cam bumps and a bit of the OD. To give you some idea of what I'm looking for (unless there's something a bunch better) I need something with perhaps a 1/2" shaft (to fit my drill) and two cones that slide over the shaft to center the cam piece bore (that the distributor shaft slides through).
Any thoughts or suggestions? This is just an experimental project at the moment so I don't want to spend serious money at a machine shop.
Thanks,
Mike