Bee Jay
Well-known member
I figured I need to move some of my projects over here. This is old but may still be helpful to someone contemplating doing this.
Bee Jay
I tried to add to a much earlier thread on this topic, but it is closed. Anyways, I finally started my batwing install this weekend. I have my trailing arms out, and I bought some offset trailing arms to replace them. They are off getting built up with new bearings.
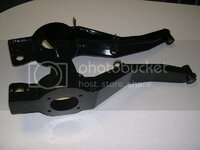
But since I have half of the rear end out, I thought now would be a good time to do the batwing install.
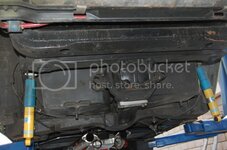
Yep, While I'm in there, the start to most Corvette projects. I'll also mount the rear end an inch higher to lower the car and it's cg.
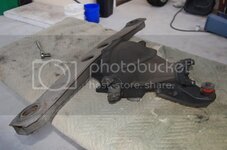
Removing the iron diff and crossmember was easy. I expected more trouble.
The batwing weighs 20 lbs. The iron cover and steel crossmeber weigh 35lbs, so I guess I'm only saving 15lbs.
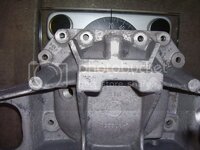
Removing the stock rubber bushings from the aluminum batwing was a major pain in the a$$. But now I know how to do it. Press the rubber out, hack saw a groove in the steel sleeve, and then chisel them out.
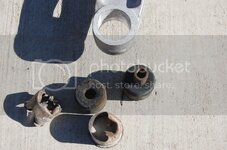
I built a tool to temporarily mount the rear end in place while I build and weld in the brackets. This tool allows me to finely adjust the height of the rear end and the batwing can be removed out of the way when it's time to weld in the brackets. You can see that the original crossmember brackets are in the way and will have to come out. I hope my sawsall can handle that. There will be no turning back, there will be nowhere to mount the original cross member.
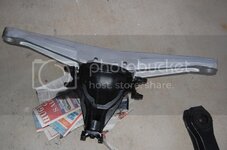
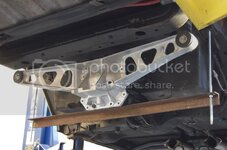
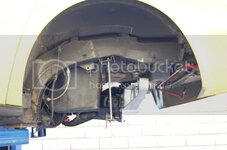
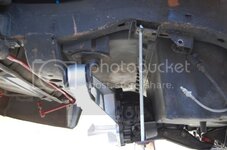
More later.
Bee Jay
The brackets are built and in. My friend Gill, we call him the "Detail Man" took Twin Turbos CAD and about a thousand measurements on my car, and designed these brackets. My friend Norm, with MAD welding skills, welded the brackets in. They are very elegant and strong. Check them out.
Hey, can somone please tell me the torque specs for the batwing cover bolts to the rear end.
Bee Jay
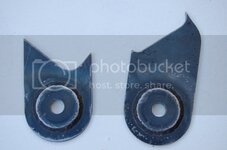
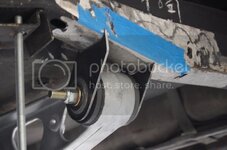
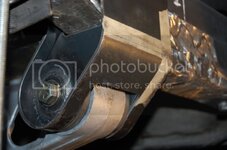
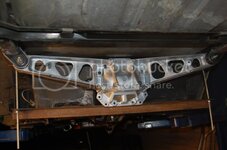
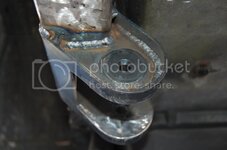
Bee Jay
Because it's there:rofl:. Also, I think it looks cool
.
It's another "while I'm in there" job, I had to remove my trailing arms to have the guts transferred to my new offset trailing arms, so I might as well do the batwing conversion while I'm in there. Actually I was hoping to raise the rear end 1" and lose about 50lbs. I ended up raising the rear end only 1/2" and I will lose 35lbs. To raise the batwing/iron rear end a full 1" higher than the original location would require modification of my hatch area floor and notching my frame for clearance. I had to trim the batwing top even with the iron rear end cover top. That gave me another 1/4" to raise the batwing. Raising the batwing to within 1/4" of the floor and 1/4" of the frame resulted in the 1/2" rise. The aluminum batwing is only 15 lbs lighter than the iron cover and crossmember, but I eliminated the crossmember that supported the rear end crossmember, just like GM did in 1980. Check this thread:
http://forums.corvetteforum.com/c3-...s-this-frame-crossmember-still-necessary.html
That crossmember weighed 20lbs. So I lost 35lbs. Here is the nose mount modified to raise 1", the washers are there to bring it back to 1/2" rise.
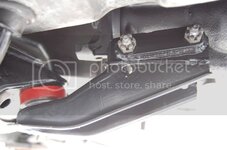
Bee Jay
The batwing is in and solidly mounted Sunday evening. After that I got the driveshaft in and called it quits. It was getting cold and my Cowboys were comming on. I'm going home to Texas for Christmas Thursday, so I'll mount the offset trailing arms and finish this whole project maybe for New Years. I want to buy and burn some of this $1.80 a gallon premium. can someone please tell me what to torque the batwing cover bolts to the rear end.
Merry Christmas everybody.
Bee Jay
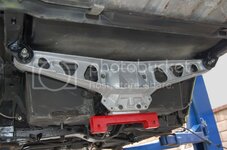
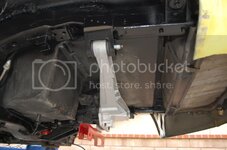
I'm back from my Christmas vacation in San Antonio Tx. It's a good thing I'm saving 35lbs with this batwing install, cause I just gained 20lbs. I got to work on the car a good nine hours today. Taking stuff apart goes much faster than putting stuff back together again. I had to raise the diff 1/4" and raise the tranny mount 3/4" to get the crank/tranny parallel with the rear end. Installing the offset trailing arms was a lotta fun, especially the bolts and alignment shims. It's important to know, the batwing mounts the leaf spring with a 3 hole plate instead of the original 4 hole plate. You must have a 3 hole plate and the needed bolts to mount the spring properly. I sure would like to know how you concours weenies put your cars together without chipping the powder coat or scratching the paint. I filled the diff with 2 pints of Valvoline synthetic gear oil. I need to bleed the brakes and hang the exhaust. Maybe tomorow after church, but the Cowoys are playing maybe their last game of the season. I need to get the car back in the garage before the rainy season gets here. Here's a pic. That batwing looks kinda cool in there. Removing that uneeded crossmember opens things up a bit too.
Bee Jay
Bee Jay
I tried to add to a much earlier thread on this topic, but it is closed. Anyways, I finally started my batwing install this weekend. I have my trailing arms out, and I bought some offset trailing arms to replace them. They are off getting built up with new bearings.
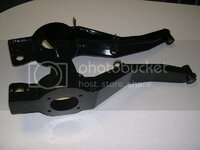
But since I have half of the rear end out, I thought now would be a good time to do the batwing install.
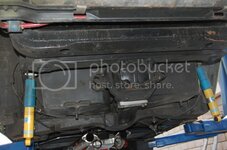
Yep, While I'm in there, the start to most Corvette projects. I'll also mount the rear end an inch higher to lower the car and it's cg.
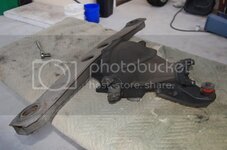
Removing the iron diff and crossmember was easy. I expected more trouble.
The batwing weighs 20 lbs. The iron cover and steel crossmeber weigh 35lbs, so I guess I'm only saving 15lbs.
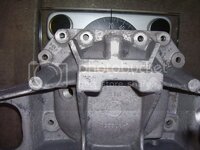
Removing the stock rubber bushings from the aluminum batwing was a major pain in the a$$. But now I know how to do it. Press the rubber out, hack saw a groove in the steel sleeve, and then chisel them out.
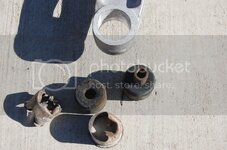
I built a tool to temporarily mount the rear end in place while I build and weld in the brackets. This tool allows me to finely adjust the height of the rear end and the batwing can be removed out of the way when it's time to weld in the brackets. You can see that the original crossmember brackets are in the way and will have to come out. I hope my sawsall can handle that. There will be no turning back, there will be nowhere to mount the original cross member.
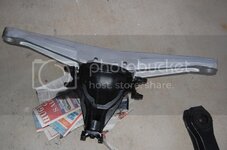
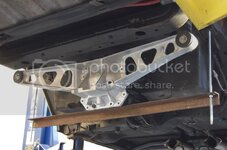
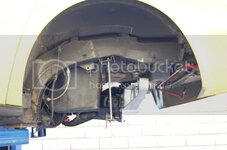
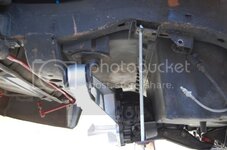
More later.
Bee Jay
The brackets are built and in. My friend Gill, we call him the "Detail Man" took Twin Turbos CAD and about a thousand measurements on my car, and designed these brackets. My friend Norm, with MAD welding skills, welded the brackets in. They are very elegant and strong. Check them out.
Hey, can somone please tell me the torque specs for the batwing cover bolts to the rear end.
Bee Jay
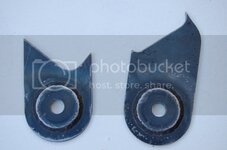
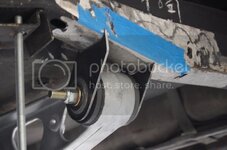
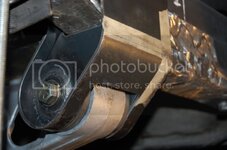
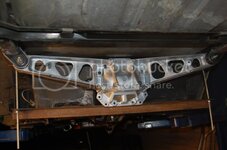
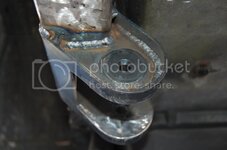
Bee Jay
Bee Jay very nice work. Just wondering why are you going through all this?
Because it's there:rofl:. Also, I think it looks cool
It's another "while I'm in there" job, I had to remove my trailing arms to have the guts transferred to my new offset trailing arms, so I might as well do the batwing conversion while I'm in there. Actually I was hoping to raise the rear end 1" and lose about 50lbs. I ended up raising the rear end only 1/2" and I will lose 35lbs. To raise the batwing/iron rear end a full 1" higher than the original location would require modification of my hatch area floor and notching my frame for clearance. I had to trim the batwing top even with the iron rear end cover top. That gave me another 1/4" to raise the batwing. Raising the batwing to within 1/4" of the floor and 1/4" of the frame resulted in the 1/2" rise. The aluminum batwing is only 15 lbs lighter than the iron cover and crossmember, but I eliminated the crossmember that supported the rear end crossmember, just like GM did in 1980. Check this thread:
http://forums.corvetteforum.com/c3-...s-this-frame-crossmember-still-necessary.html
That crossmember weighed 20lbs. So I lost 35lbs. Here is the nose mount modified to raise 1", the washers are there to bring it back to 1/2" rise.
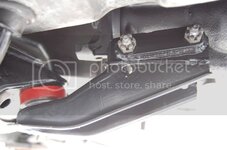
Bee Jay
The batwing is in and solidly mounted Sunday evening. After that I got the driveshaft in and called it quits. It was getting cold and my Cowboys were comming on. I'm going home to Texas for Christmas Thursday, so I'll mount the offset trailing arms and finish this whole project maybe for New Years. I want to buy and burn some of this $1.80 a gallon premium. can someone please tell me what to torque the batwing cover bolts to the rear end.
Merry Christmas everybody.
Bee Jay
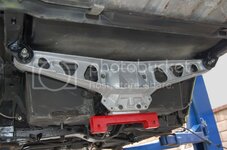
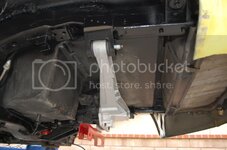
I'm back from my Christmas vacation in San Antonio Tx. It's a good thing I'm saving 35lbs with this batwing install, cause I just gained 20lbs. I got to work on the car a good nine hours today. Taking stuff apart goes much faster than putting stuff back together again. I had to raise the diff 1/4" and raise the tranny mount 3/4" to get the crank/tranny parallel with the rear end. Installing the offset trailing arms was a lotta fun, especially the bolts and alignment shims. It's important to know, the batwing mounts the leaf spring with a 3 hole plate instead of the original 4 hole plate. You must have a 3 hole plate and the needed bolts to mount the spring properly. I sure would like to know how you concours weenies put your cars together without chipping the powder coat or scratching the paint. I filled the diff with 2 pints of Valvoline synthetic gear oil. I need to bleed the brakes and hang the exhaust. Maybe tomorow after church, but the Cowoys are playing maybe their last game of the season. I need to get the car back in the garage before the rainy season gets here. Here's a pic. That batwing looks kinda cool in there. Removing that uneeded crossmember opens things up a bit too.
Bee Jay
Last edited: