enkeivette
Well-known member
- Joined
- Mar 30, 2008
- Messages
- 990
So I noticed today as I was finishing up the sanding, that my headlights won't open. The headlights will now hit the body behind them, if I push down on the body (area behind the headlights in front of the hood) there is enough room for them to lift. So after examining I realize that the body has somehow separated from the metal brace underneath it. I'm assuming it's glued? How can I fix this? Countersunk screws through the body, into the metal and filler over the screws? Or should I just glue it? What sort of glue if so?
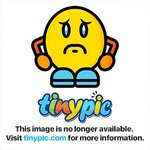
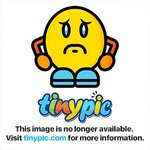
Last edited: