69427
The Artist formerly known as Turbo84
A few of you might remember some frame modeling I did a while back to try some ideas I was kicking around to stiffen up the spare '69 frame of mine.
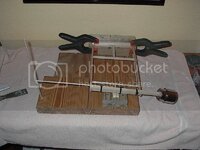
Got most of the frame tweaks done, and am spending some time twisting the frame looking for areas I missed. So far it's pretty amusing, but I'm warping the crap out of my anchor point (my car hoist), which is gumming up my measurements. I'm trying to look at this positively, as the frame does appear to be transferring the torque from the front moment arm back to the lift anchor area. I'm doing a couple changes to the anchor area trying to stiffen up that part of the lift runner. I've got the rear of the frame clamped (by the batwing mounts) to the lift runner, and using the car weight to help keep things from moving around. (Plus, I didn't want to have to push the car in and out of the garage.)
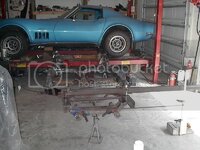
I'm using a seven foot moment arm, mainly because I can't close the garage door if I use anything longer. With my weight, and the weight of the arm, I'm putting 1500 lb-ft of torque on the frame during these initial tests. Once I get the anchor area stabilized, I'll hang some additional weight on the arm to try to get to 2000 lb-ft. It's hard to see in the picture, but I'm using another small arm and a yardstick to make the deflection measurements, and then will have to blow off the cobwebs from what I learned in 8th grade geometry to calculate the angles and such.
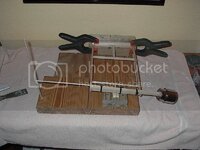
Got most of the frame tweaks done, and am spending some time twisting the frame looking for areas I missed. So far it's pretty amusing, but I'm warping the crap out of my anchor point (my car hoist), which is gumming up my measurements. I'm trying to look at this positively, as the frame does appear to be transferring the torque from the front moment arm back to the lift anchor area. I'm doing a couple changes to the anchor area trying to stiffen up that part of the lift runner. I've got the rear of the frame clamped (by the batwing mounts) to the lift runner, and using the car weight to help keep things from moving around. (Plus, I didn't want to have to push the car in and out of the garage.)
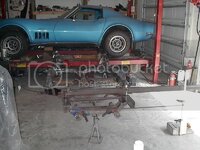
I'm using a seven foot moment arm, mainly because I can't close the garage door if I use anything longer. With my weight, and the weight of the arm, I'm putting 1500 lb-ft of torque on the frame during these initial tests. Once I get the anchor area stabilized, I'll hang some additional weight on the arm to try to get to 2000 lb-ft. It's hard to see in the picture, but I'm using another small arm and a yardstick to make the deflection measurements, and then will have to blow off the cobwebs from what I learned in 8th grade geometry to calculate the angles and such.